T2000 Series Induct-A-Ring Shaker Systems
The T2000 Series of vibration test systems is designed to meet the ever-changing challenges of today’s moderate to extreme level test requirements. The T2000 Series is used by many different industries with a proven track record of unmatched and as yet unchallenged performance and long term reliability.
Features
- 15,000 - 25,000 lbf (67 - 111 kN) peak sine
- 15,000 - 24,000 lbf (67 - 107 kN) RMS random
- Extreme performance:
- Sine - 200 g
- Shock - 600 g
- High SRS Shock - 2,000g @ 5,000 Hz
- Induct-A-Ring (IAR) armature
- Armature weight with inserts 100 lbs (45.4 kg)
- 17.5 inch (445 mm) diameter armature
- 2 inch (51 mm) stroke; 3 inch (76 mm) stroke optional
- Three base configurations:
- Modular, high-efficiency class D power amplifier
- Ultra-rugged, reliable Silicon Carbide (SiC) MOSFET Technology
- Combined environment support
- Variable Speed Blower option
- APEX SL Control Systems
- Command Link APEX SL / Amplifier remote interface
Induct-A-Ring
The Induct-A-Ring (IAR) armature is part of an advanced shaker design available only from Unholtz-Dickie. This unique solid metal armature provides electrical simplicity and mechanical durability benefits (not available with traditional armature designs) that together make the T2000 Series Systems the most reliable, high-performance shaker systems in the world.
T2000 IAR Features
- Solid aluminum armature coil (no multiple windings)
- Low weight: 100 lbs (45 kg)
- Superior strength
- Large table diameter 17.25 inches (445 mm)
- All points at ground potential
- No electrical current connections
- No cooling water connections
- 29 stainless steel replaceable inserts
- 2 Inch pk-pk displacement; 3 inch (76 mm) optional
- Rated acceleration: 200 g sine / 600g shock
Competitive shakers utilize wound coil armatures which are cheaper to produce, and are less reliable under high-stress conditions (structural and thermal). Wound coil shaker designs are acceptable for low force applications, but are inadequate when used in higher force applications.
Induct-A-Ring vs Conventional Armature Design | ||
---|---|---|
UD T2000 Induct-A-Ring | Conventional Shaker Design | |
Armature Construction | ![]() Solid metal, forged aluminum ring bolted to upper casting. |
![]() Insulated copper wire is held together with epoxy joints. Armature is epoxy bonded to upper casting. |
Electrical Connection | Inductively coupled – No electrical current leads required. All points on moving armature remain at ground potential. | Fragile 1000 Amp current connection bridging shaker suspension required. Armature is at high voltage potential. Voltage break down and shorting (arcing) are possible. |
Armature Cooling | Air-cooled – simple and effective | Design requires fragile water connection to bridge the armature suspension to cool the coil. These hoses and fittings are subjected to high vibration stress. |
Armature Weight | 100 lb (45 Kg) moving element. Solid metal construction and reduced weight provide superior strength to weight ratio, a key factor for high performance and reliability. | >125 lbs (57 Kg) moving element (typical). Many individual components, potentially weak epoxy joints and non-rigid structures. |
Rated Acceleration | 200 g sine / 600 g shock | 100 - 150 g max sine |
Rated Stroke | 2 inches pk-pk (51 mm) 3 inches (76 mm) optional |
1.5 to 2 inches pk-pk (38 - 51 mm) - max |
High Reliability
Induct-A-Ring technology has substantially improved shaker armature reliability by combining mechanical durability and electrical simplicity. Most conventional armatures utilize a complicated armature construction of electrical windings, epoxy bonded joints, high amperage flexures (to deliver input power to the coil), and high pressure hoses (to bring cooling water in and out of the coil). Each of these components is subjected to the same vibration and/or shock levels applied to the test specimen. Repeated high level operation often leads to fatigue failures, water leaks, cracked epoxy joints, burned out windings, or voltage breakdown in the coil.
By comparison, the INDUCT-A-RING armature is a simple two-piece metal structure. No electrical current leads or water cooling connections are needed. There are no electrical windings. All points on the armature are at ground potential at all times. There is no possibility of voltage breakdown. No electrical insulation is utilized anywhere in the armature assembly because there is zero voltage potential between any two points on the ring, and between the ring and ground.
Consider an armature consisting of two rigid members bolted together versus a structure made up of an assortment of electrical windings clamps, flexing leads, and hoses. Which design would you expect to deliver 200g sine operation and 600g shock pulses without sacrificing armature reliability? The answer is Induct-A-Ring.
Performance
The T2000 Series was designed to operate over a wide force range covering moderate to extreme test conditions and accommodating small to large test payloads. Internal pneumatic load support permits automatic armature re-centering for full stroke capability with payloads up to 1,900 lbs (863 kg). External load support can augment this capability for very large test packages. The T2000 Series is used in many demanding applications for the Automotive, Commercial, Industrial and Military sectors.
Variable Speed Blower
An optional Variable Speed Blower feature is available that automatically controls cooling blower RPM as a function of power amplifier output current (system force). At low test levels and for most shock tests, the blower spins at a significantly reduced rate (if at all), providing a large reduction in power consumption, acoustic noise and air volume extracted from the lab area.
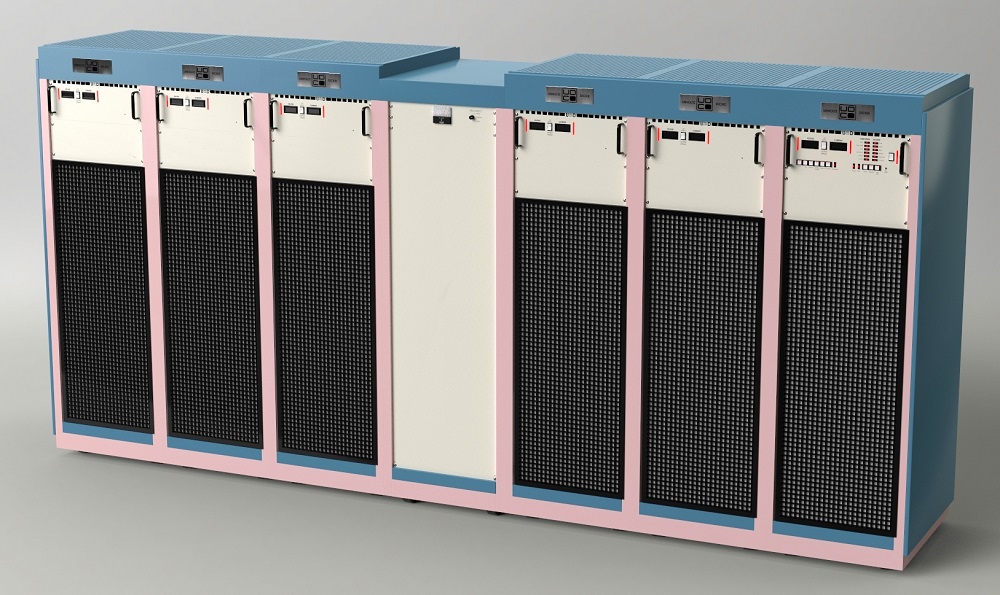
Power Amplifiers
T2000 Series systems utilize high efficiency SC-Series class D power amplifiers. These amplifiers are built as complete power centers including EMI shielded console, 3 phase line filtering, full featured control panel, integrated safety interlocks, DC field supply and interconnect cabling with military grade connectors. The amplifiers are completely air-cooled and modular in design, configured from 125 up to 725 KVA. The compact design accommodates up to 125 KVA output in a single bay console.
For installations combined with environmental temperature chambers, a remote interface allows automatic system startup from a single contact closure. All SC Series amplifiers are direct-coupled to the shaker and require no transformer tap re-connections or special switching circuits to achieve full rated system performance. SC Series amplifiers are also often supplied as replacements for older style or less efficient amplifiers.
- Air cooled, modular 65-725 KVA
- Ultra-rugged Silicon Carbide (SiC) Transistor Technology
- Automatic sensing of sine or random drive inputs
- Fast-acting shutdown circuitry
- 90% efficiency
- Adjustable limits
- EMI shielded consoles
- Input AC power line filtering
- Expandable output ratings
- Full interlock status for amplifier, shaker and cooling package